Qiang Qin*
School of Earth Science and Engineering, Xi’an Shiyou University, Xi’an 710065, China
*Corresponding email: qinqiang@cosl-expro.com
https://doi.org/10.71052/srb2024/bzrz3059
Abstract
This paper provides a comprehensive review of the methods and techniques developed over the past two decades for optimizing continuous gas lift systems. It traces the evolution from isolated single-well analysis to real-time, multivariate optimization approaches that consider the interactions of all wells in an oilfield. While some methods are limited by their failure to account for the interdependencies among well sharing common streamlines, others struggle with scalability and the quality of solutions when applied to large-scale networks of hundreds of wells. The aim of this paper is to offer insights into the development of gas lift optimization methods and highlight the key challenges that remain unresolved in the field.
Keywords
Gas field development, Gas production operation, Gas lift, Process optimization
Introduction
Artificial gas lifting is a common method used to enhance production from non-producing or low-producing wells. In this technique, natural gas is injected at high pressure into the wellbore, where it mixes with the reservoir fluid. This continuous aeration process reduces the effective density of the fluid, thereby lowering the hydrostatic pressure of the liquid column. As a result, the flowing bottom-hole pressure (Pbh) decreases, increasing the pressure differential (Pr – Pbh) between the field reservoir pressure (Pr) and the bottom hole pressure. This enhanced pressure difference facilitates the upward flow of produced fluid to the surface [1,2]. This method is cost-effective, durable, and versatile, working effectively under a wide range of conditions. However, it assumes a stable and sufficient supply of lifting gas. At a certain point, the benefits of reduced static pressure are offset by increased frictional losses caused by the large volume of gas in the wellbore. These frictional losses can lead to higher bottom-hole pressures, which, in turn, reduce liquid production. As a result, each well has an optimal gas-lift injection rate [3,5].
When considering the entire gathering and transportation network, the optimal gas-lift injection rate for a single well differs from the rate that maximizes production for that well alone. This discrepancy is due to the back-pressure effect exerted by downstream wells, which increases pressure losses along the gas production line due to the common tie-back [6]. As oil fields mature and infrastructure becomes more constrained, the demand for gas lift increases. However, operational limitations—such as compression capacity, gas availability, and well shut-ins—can prevent the realization of maximum production potential. In the absence of operational constraints, it is necessary to optimize the distribution of available lifting gas across multiple wells to maximize overall production. This forms the basic definition of the gas-lift optimization problem, which can be seen as an optimal allocation problem [7].
With the introduction of additional operational restrictions, including throttling control, well-speed management, and challenges related to workovers and well treatments, a broader definition of the problem has emerged. Both definitions of the optimization problem can be adapted to an economic objective function that factors in production and injection costs. While the choice of objective function may vary across different methods, most approaches are flexible enough to handle any problem definition and should not be classified based solely on this criterion.
Historically, the solutions to this problem have evolved over time, starting with the generation of gas-lift dynamic curves from well-test data, followed by single-well node analysis and sensitivity studies. This was followed by models based on quasi-steady-state curves that ignored interactions, steady-state solutions using network simulators, and coupled reservoir-surface facility simulations. Ultimately, the field has progressed to fully integrated asset modeling techniques.
Gas well lifting performance
The actual well investigation involves physical well testing at the well site. Fluid composition, PVT and other related tests provide information about the well condition and its potential productivity. In addition, the step rate gas injection test can accurately describe the liquid production behavior injection with the increase of gas lift. The nature of injecting single well test naturally leads to the development of tools to simulate the behavior of single well, and given certain input parameters to define completion, fluid composition, pressure and temperature at wellhead and contact point with reservoir. These nodal analysis tools can define the calculation model of oil well by simple black oil or more detailed component fluid description, starting from sand layer, passing through perforation hole, from bottom hole, passing through tubing, reaching wellhead, and then from downstream to conveying water tank [8]. The model can be used to predict multiphase flow through oil wells, and the more representative the model is, the better. Therefore, in order to overcome the complexity of high-cost and time-consuming step rate testing in oil fields with multiple wells, these tools can be used to provide lifting performance curves of all lifting wells. Obviously, single well analysis provides an incomplete picture of the whole oilfield performance, especially for the optimal gas lift configuration. However, it has two important purposes.
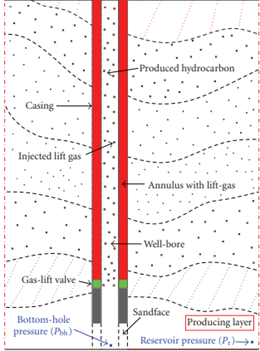
Figure 1. Schematic diagram of gas lift well.
First of all, all network simulators are based on such a single well model, coupling the behavior of a single well in an oil field through a common gathering and transportation network. That is to say, when solving the network solution, the node analysis tool is used to calculate the potential multiphase fluid flow behavior. Secondly, in the absence of actual step rate test data, the lifting performance curves are estimated by running the sensitivity model for each individual. Well, yes, these gas lift performance curves are used for gas lift optimization research. This is correct when the influence of interdependent wells is considered through the updated lifting performance curve under new conditions, but it is wrong when the obtained pseudo-steady-state solution is accepted only after one cycle. The latter is a common assumption in many papers, usually for the sake of simplicity, if not for negligence. The complete, or final, steady-state solution is a solution derived from the network simulator. In the network, after the lifting gas is distributed to the network, strict pressure balance is achieved at all nodes in the network. This is necessary because the back pressure exerted by the lifting gas injected into one well will affect the production of all connected wells. Therefore, in order to obtain the best output, it is necessary to properly distribute lifting gas while considering engineering modeling and simulation.
Single well analysis
Hari et al. proposed a more accurate model based on the balance of mass, energy and momentum [9]. Taking a single well as an example, the commercial optimization program based on mixed interior point algorithm is used to determine the gas injection depth, pressure and gas injection volume. It is reported that the results are more accurate than the standard node method, so it is more suitable for field simulation research. However, there is no report on the results of field application. Note that it is also recommended to use the component model on the simple black oil model to improve the accuracy. In fact, the best model to produce representative gas lift dynamic curve is an ideal simulation and optimization purpose. Sahu et al. used node analysis method to study the injection of lifting gas into a single well [10]. Before investigating 13 well patterns, the influence of gas injection on back pressure of two wells was considered. It is pointed out that the single well method is not enough to analyze the production network of multiple gas lift wells, so a general network solver is necessary. That’s right, systematically optimize wells, but on the basis of wells, there will be no guarantee that an optimal solution will get the whole network. Similarly, Sreenivasan et al. pointed out that accurate estimation of gas injection and liquid production is needed for oilfield-wide optimization [11], but more importantly, because the conditions of one well will affect other connected wells, computer simulation is needed to effectively explain the interaction. This cannot be done manually. The remote controller is used to control the gas injection speed of gas lift in real time, which can maximize the output, reduce the cost and reduce the blockage caused by pipeline freezing. Accurate flow and injection measurements are considered necessary to ensure accurate model interpretation and optimization, and also to ensure the stability of heading and slug effect. The single well optimization scheme adopts unconstrained optimization, which does not limit the supply of gas lift, or determines the injection rate of maximum production under the condition of operational constraints (including the available amount of gas lift). The formation of hydrate, low ambient temperature, and the change of lifting gas supply, pressure or quantity may lead to unsatisfactory gas injection level, which may lead to the decline of cumulative oil well productivity. Continuous monitoring and continuous optimization are considered essential to ensure that the oil well runs at maximum efficiency most of the time, thus significantly increasing the total output. It should be pointed out that in order to connect multiple oil wells, more complex optimization programs are needed to deal with the interrelated oil well allocation problems. Although only one well is considered, and the optimization scheme is limited to setting the gas lift rate that leads to the highest flow, the elements needed for remote real-time field gas lift optimization are obvious.
Network-based solutions
A series of different WHP lifting performance curves is generated for each well. The ground gas lift assembly is modeled in the network simulator, including the detailed compressor model. The curve is assumed to be piecewise linear and optimized by SLP method. The separator pressure, gas lift header pressure and gas lift injection rate are taken as control variables. This method is tested on two configurations of compound model based on four oil fields (including 40 production platforms and 200 wells) to maximize the income under the constraints of equipment and network. This method can deal with large-scale complex ring networks and constraints at the same time. A lot of research has been done, including the shutdown of gas-lift compressor unit, the determination of gas-lift injection pressure and the evaluation of gas transmission across oil fields. It is pointed out that it is difficult to determine the gas lift performance curve at low injection rate, which affects the solution quality. Generally speaking, compared with the single production pipeline model, the addition of natural gas compression and gas injection system enhances the overall advantages of the optimized solution.
The latter performs local search and keeps a set of search points marked as feasible, which is called taboo step. The search is moving in the most likely direction of improving the objective function. This method has been tested in a 25-well system, and production has increased by 5% compared with the original state. The system considered includes a production well, a surface facility model and several operational constraints. Although other forms of artificial lifting (rod pump and submersible pump) are considered, this scheme is also suitable for gas lift. The main disadvantage of this method is that the cost of function estimation is high because of the scheme based on global randomness.
However, DP algorithm approximately solves the discrete gas lift optimization problem by using priority constraints. The results showed some cases ranging from 6 to 48 wells. The DP algorithm is relatively fast. Although this method is approximate, it provides a near-optimal solution for medium-sized networks (10-20 wells) through discretization of a large enough model. Generally speaking, the proposed formula is NP-hard (which refers to the complexity of uncertain polynomial time hard algorithm), which shows that with the increase of dimension, the complexity caused by the increase of connected graph size cannot be effectively solved.
Conclusion
In the oil field, due to the limitation of facilities, the available lifting gas is easy to change every day. In addition, operating conditions and treatment facilities can determine the capacity of compressor and the limitation of separator in the production process, and improper distribution of available lifting gas may cause economic costs, which may lead to excessive constraints or over-design of facilities. Therefore, the best gas lift configuration is desirable to ensure the best oil production or profit.
In this paper, the solving methods of continuous gas lift optimization problems are summarized. Although the basic problem involves the optimal allocation of gas lift, the broader problems can also include well speed management and well strategy. The former involves the pressure and flow control of downhole throttle valve, and the latter involves the activation state or connection of well. In some cases, the design of the gas lift well is also considered together with gas injection speed.
Therefore, although some methods are more robust and can be extended to large-scale production-limited oil fields consisting of hundreds of wells with a large number and types of variables, others are obviously limited. Classical single well analysis ignores the interaction of other wells in the oilfield, curve model ignores the back pressure effect of connected wells, and network-based simulation ignores the influence of reservoir and process facilities model. For the latter full-field simulation, the above scheme is very important to ensure the speed, stability and universality of the real-time optimization solution on the fast inner loop, while the slow outer loop can adapt through the time step of the inner loop.
In this case, the successful control and optimization of the inner loop is a necessary prerequisite for the composite full-field integration solution. Therefore, the method designed to ensure this must be able to deal with large oil fields, difficult and non-instantaneous flowing wells, and provide accurate approximate optimal solutions within a reasonable time under many operational constraints. In other words, they should be able to monitor oil wells without intervention and provide solutions when the operating conditions are unlikely to change significantly. In this respect, the hierarchical optimization method may be preferred rather than the integrated method. Please note that when the coupling simulation includes a reservoir model that is not based on decline curve, the rigor of the coupling scheme and any amplification program adopted will affect the cost of objective function evaluation and ultimately affect the quality of the obtained results. However, like any enterprise, the model should be able to represent the system of interest and be robust to achieve the purpose of actual optimization.
What is outlined above is to optimize the whole coupling or integration system during the simulation period of interest. Due to the cost associated with the evaluation of a single objective function, which is achieved by using a derivative-free method, some cost is still needed, or, more practically, an agent-based method is used. In this paper, a fast analytical approximate model is established from representative sample sets by using neural network, kriging or radial basis function method. Then the approximate model is used to replace the actual simulation model in the optimization step. The advantage of iterative proxy scheme is to further reduce the number of iterations of expensive function evaluation required for sampling only in the perceptually optimal region of each node. These methods have been proved to be robust, but they are often limited to the practical reasons of the dimensions of dozens of variables.
Acknowledgement
This work was not supported by any funds. The authors would like to show sincere thanks to those techniques who have contributed to this research.
References
[1] Sahu, C., Kumar, R., Sangwai, J. S. (2021) A comprehensive review on well completion operations and artificial lift techniques for methane gas production from natural gas hydrate reservoirs. Energy & Fuels, 35(15), 11740-11760.
[2] Sreenivasan, H., Patel, J., Jain, D., Patel, S., Wilson, I., Krishna, S. (2024) Optimization of gas lift system for well performance improvement in Asmara formation: A techno-economic perspective. Petroleum Research, 9(1), 115-124.
[3] Okorocha, I. T., Chanukiah, C. E., Memona, C. E., Memona, C. O. (2020) Gas lift optimization in the oil and gas production process: a review of production challenges and optimization strategies. International Journal of Industrial Optimization, 1(2), 61-70.
[4] Santos, O. G., Bordallo, S. N., Ahanti, F. J. (2001) Study of the dynamics, optimization and selection of intermittent gas-lift methods—a comprehensive model. Journal of Petroleum Science and Engineering, 32(2-4), 231-248.
[5] Syed, F. I., Alhamdi, M., Dah Aghi, A. K., Nagappan, S. (2022) Artificial lift system optimization using machine learning applications. Petroleum, 8(2), 219-226.
[6] Al-Mansory, S. H. O., Al-Fallaci, O., Kadkhoda, A. (2024) Gas Lift Optimization for Zubair Oil Field Using Genetic Algorithm-Based Numerical Simulation: Feasibility Study. Iraqi Journal of Chemical and Petroleum Engineering, 25(2), 161-174.
[7] Abu-Bakri, J., Jafari, A., Namdar, H., Ahmadi, G. (2024) Increasing productivity by using smart gas for optimal management of the gas lift process in a cluster of wells. Scientific Reports, 14(1), 15489.
[8] Al-Janai, M. A., Mahmood, H. A., Al-Fallaci, O. F., Sadeq, D. J., Al-Jumaah, Y. M., Essa, A. A. (2024) Optimizing Gas Lift for Improved Oil Recovery in a Middle East Field: A Genetic Algorithm Approach. Journal of Petroleum Research and Studies, 14(3), 52-74.
[9] Hari, S., Krishna, S., Patel, M., Bhatia, P., Vij, R. K. (2022) Influence of wellhead pressure and water cut in the optimization of oil production from gas lifted wells. Petroleum research, 7(2), 253-262.
[10] Sahu, C., Kumar, R., Sangwai, J. S. (2021) A comprehensive review on well completion operations and artificial lift techniques for methane gas production from natural gas hydrate reservoirs. Energy & Fuels, 35(15), 11740-11760.
[11] Sreenivasan, H., Patel, J., Jain, D., Patel, S., Wilson, I., Krishna, S. (2024) Optimization of gas lift system for well performance improvement in Asmara formation: A techno-economic perspective. Petroleum Research, 9(1), 115-124.
Share and Cite
Qin, Q. (2024) A Comprehensive Review of Gas Lift Optimization Methods. Scientific Research Bulletin, 1(2), 4–9. https://doi.org/10.71052/srb2024/bzrz3059